If you’re considering TPO roofing for your building, you may be asking whether or not it requires underlayment. The answer to this question is not a simple yes or no. It depends on a few different factors.
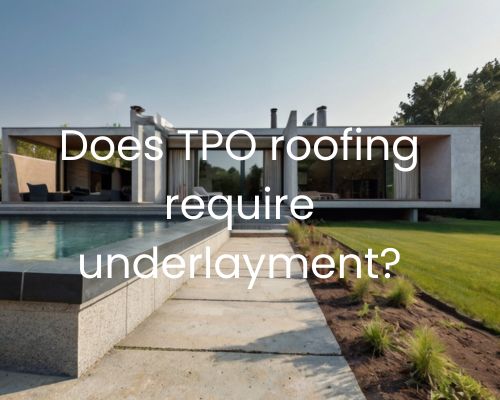
First, it’s important to understand what TPO roofing is. TPO stands for thermoplastic olefin, which is a type of single-ply roofing material. TPO roofing is commonly used on commercial and industrial buildings. It is known for its energy efficiency, durability, and ease of installation. It is typically installed in large sheets that are welded together to create a seamless, watertight barrier.
When it comes to underlayment, TPO roofing does not necessarily require it. However, there are some situations where underlayment may be recommended or required.” said Charles Jimerson of Commercial Roofing NJ.
For example, if the roof deck is uneven or in poor condition, an underlayment may be necessary to create a smooth surface for the TPO membrane to be installed on. Additionally, some building codes or roofing manufacturers may require the use of a specific type of underlayment with TPO roofing.
Understanding TPO Roofing
If you are considering TPO roofing for your commercial or residential property, it is important to understand the composition and installation process of this type of roofing. TPO, or Thermoplastic Polyolefin, is a single-ply roofing membrane that is known for its energy efficiency, durability, and lightweight properties. In this section, we will explore the characteristics of TPO roofing, the installation process, and the advantages of using TPO roofing.
Composition and Characteristics
TPO roofing is made up of a blend of synthetic materials, including ethylene propylene diene monomer (EPDM), polyvinyl chloride (PVC), and chlorinated polyethylene (CPE). The TPO membrane is typically white, which helps to reduce heat absorption and reflect sunlight, making it a popular choice for cool roofs. TPO roofing is also environmentally friendly and recyclable.
Installation Process
Before installing TPO roofing, you need to make sure that the roof deck is clean, dry, and free of debris. Then, you can roll out the TPO membrane carefully. Make sure to pay attention to proper alignment and overlap areas for welding. The seams are heat welded together, creating a strong and durable bond. Fasteners are used to secure the TPO membrane to the roof deck, and flashing is installed around the edges and any penetrations.
Advantages of TPO Roofing
TPO roofing offers many advantages over other types of roofing materials. It is cost-effective, energy-efficient, and durable, making it a popular choice for commercial and residential properties. TPO roofing is also flexible and can withstand extreme temperatures, making it ideal for use in areas with harsh weather conditions. Additionally, TPO roofing is resistant to UV radiation and can reflect solar heat, which can help to reduce energy costs.
TPO Roofing System Details
Underlayment Necessity and Alternatives
TPO roofing systems are known for their durability, energy efficiency, and ease of installation. One common question that arises is whether TPO roofing requires underlayment. The answer is that it depends on the specific roofing project and the building’s needs.
While TPO roofing systems do not require underlayment, a slip sheet or separation layer may be used on top of the roof to protect the membrane from abrasion due to rooftop equipment or exposure to chemicals. Additionally, some building codes may require underlayment for specific roofing projects.
If underlayment is necessary for your TPO roofing system, there are a few alternatives to consider.
One option is to use a vapor barrier as an alternative to traditional underlayment. Another option is to use insulation as an underlayment alternative, such as polyiso insulation. Your professional roofer can help you determine the best underlayment option for your specific roofing project.
Maintenance and Repair Considerations
Like any roofing system, TPO roofing systems require regular maintenance and occasional repairs. It is important to have your TPO roofing system inspected regularly by a professional roofer like Commercial Roofing NJ to identify any potential issues before they become major problems.
Common maintenance tasks for TPO roofing systems include cleaning the roof surface, removing debris, and inspecting seams and flashings. If you notice any leaks or punctures in your TPO roofing system, make sure to have them repaired as soon as possible to prevent further damage.
Cost Analysis and Warranty Information
When considering a TPO roofing system, it is important to consider the cost and warranty information.
The cost of a TPO roofing system can vary depending on factors such as the size of the roof, the labor costs, and the roofing materials used.
However, TPO roofing systems are generally considered cost-effective due to their energy efficiency and longevity.
TPO roofing systems can last anywhere from 15 to 40 years, depending on a number of variables.
Additionally, many TPO roofing systems come with warranties that can cover defects in materials or workmanship.
Be sure to read and understand the warranty information before installing a TPO roofing system to ensure that you are covered in the event of any issues.
Overall, TPO roofing systems are a popular choice for commercial buildings due to their durability, energy efficiency, and ease of installation.
With proper maintenance and repair, a TPO roofing system can provide reliable protection for many years to come.